Material Handling System TECHNOLOGY
Examples of Upgrading Remotely-Controlled,
Automated RTGS with customization incorporating user needs.
Automatic Rubber Tired Gantry Crane
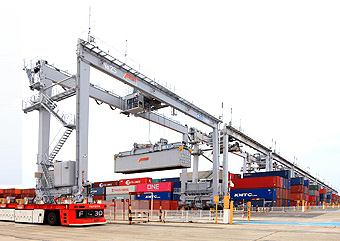
Realizing safe and stable container handling operations by improving operator working conditions.
In 2005, we were the first in the world to successfully put into commercial operation, remotely-controlled, automated RTGs thereby vastly improving working conditions for their operators. By seemlessly integrating both automated and remote-control operation, a high level of operational efficiency was obtained and our comprehensive safety sensing functions have greatly contributed to safety and stable operation.
- KEYWORD
-
- #Automation
- #Efficiency
- #Improving the Working Environment
- #Remote Operation
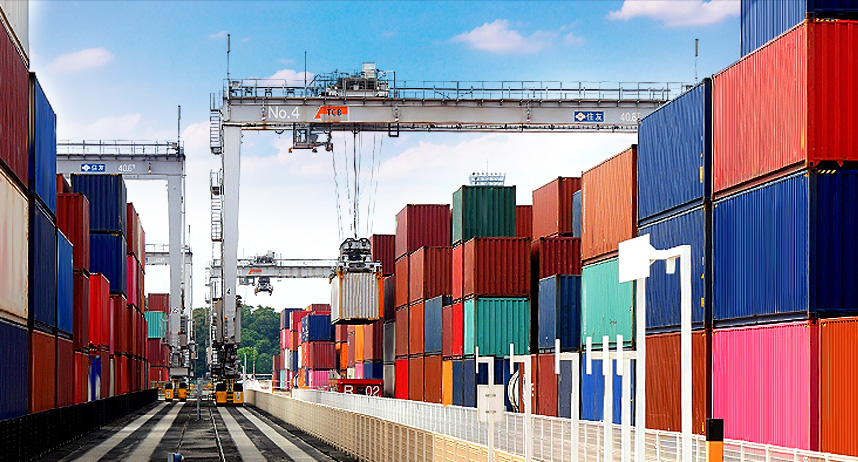
Example of Upgrading Target Sensing
Up to now:
Use of image processing to directly detect target position to obtain container stacking accuracy within ±35mm.
Now:
Adding 2D scanners to image processing to enhance relaibility.
We have increaed container stacking accuracy by comparing the results of Magic-Eye sensing and the 2D scanner to stop container stacking when discrepancies between these two systems are detected.
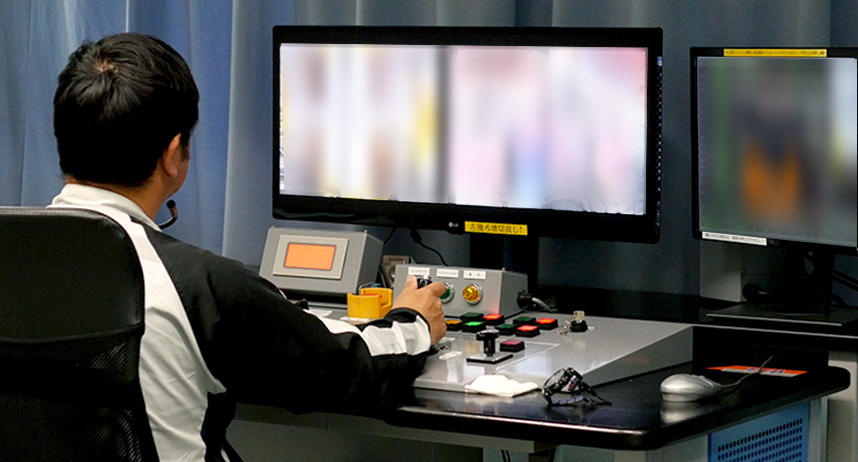
Upgrading the Remote Operating Station
Incorporating advanced designs and customizing in accorcance with customer requirements.
First Generation:
Remote Operating Station using analog CRT Displays, The control desk was of wood construction with built-in control panels.
Second Generation:
Simplified design using high resolution digital displays.
The desk surface was made flat, with angled displays and used colors more suited for an office style environment (from black to white).
Third Generation:
Use of 4K Digital Displays for increased resolution.
All graphics and images were grouped in one display with all buttons and lamps changed to round, flush fitting type to maintain a flat surface.
Upgrading the RTG Runway Safety Surveillance System
This system consists of two dissimilar surveillance systems, LiDAR (3-D scanner) and TOF (Time of Flight 3-D sensor).
We have developed our own RTG Runway Obstruction Detection System using LiDAR. This system can detect obstructions on the RTG runway even if the RTG is leaning forwards due to inertia of gantry travel. We also use TOF 3-D Sensors to detect obstructions in the same area, to ensure positive detection.
Upgrading Container Stacking Accuracy
We have developed means of automatically stacking containers on cambered ground by slightly shifting each stacking level horizontally to maintain a vertical stack.
This function solves the problem of stacking on cambered ground which results in a tilted stack, making it difficult to stack containers in the adjacent stacks.
Upgrading wireless transmission
High Capacity Wireless Transmission
At first, high capacity, high speed transmission of voluminous image data was done by analog VHF wireless method by using a leakage coaxial cable, but for the next stage of development, we switched to digital transmission via leakage coaxial cables.
We have now progressed to enable high-speed, high-volume wireless transmission using a 5G transmission system.
First Generation (2005 - 2016): Analog image transmission
Development of analog wireless image transmission using leakage coaxial cables.
Second Generation (2016 - 2021): Digital image transmission
Digital wireless image transmission using leakage coaxial cables.
The Latest (2021 onwards): High speed, high-volume 5G wireless transmission.
PRODUCT LIST
MENU